Embarking on a roller coaster project can be an exhilarating venture, blending creativity, engineering, and a keen understanding of the materials involved. The selection of materials is critical to the success and safety of any roller coaster, influencing not just the ride experience but also its longevity and reliability. This guide delves into the essential materials used in constructing modern roller coasters, providing insights that draw from both industry expertise and a commitment to quality and safety.
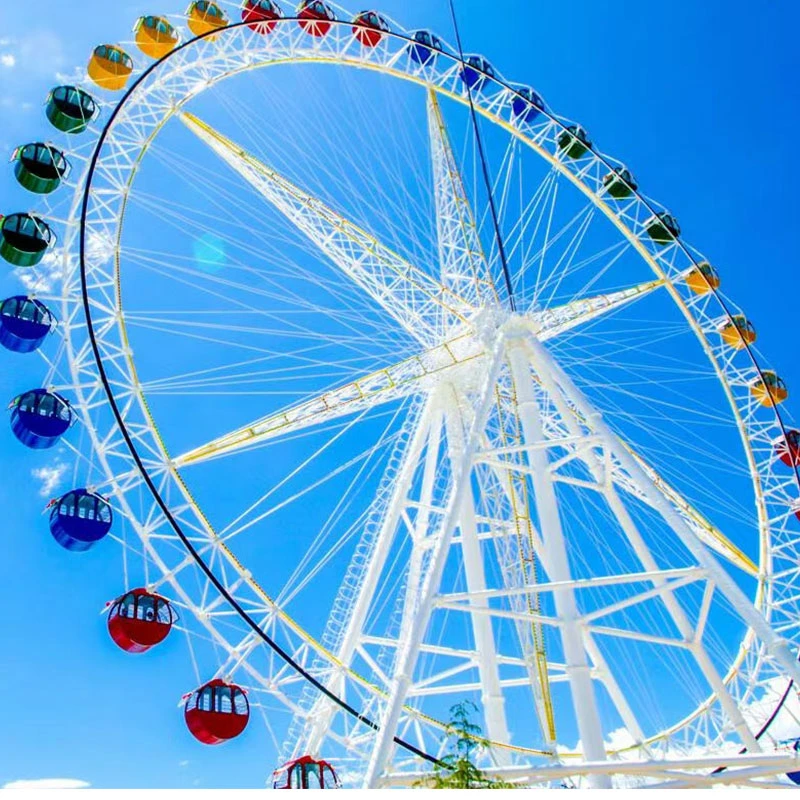
Steel, without a doubt, is the backbone of modern roller coasters. Its versatility allows for the creation of intricate loops, twists, and turns that define the thrill of a ride. Steel is prized for its strength and durability, capable of withstanding the immense forces and wear exerted by daily operations. Its corrosion-resistant properties ensure that structures remain safe and aesthetically pleasing over time, reducing maintenance costs and extending the coaster’s lifespan. Engineers often employ specialized grades of steel, such as high-strength, low-alloy steel, to further optimize performance and safety.
Wood, though traditional, continues to play a significant role in the roller coaster world. Wooden coasters offer a unique ride experience, noted for their classic, rickety feel and the nostalgia they evoke. Despite newer materials entering the arena, wood’s natural flexibility and resilience make it ideal for absorbing vibrations and loads during operation. However, maintaining wooden coasters requires a more hands-on approach, including regular inspections and treatments to prevent decay and damage from the elements. The marriage of steel and wood, seen in hybrid coasters, melds the charm of wooden rides with the benefits of steel, delivering an engaging ride experience that resonates with enthusiasts and operators alike.
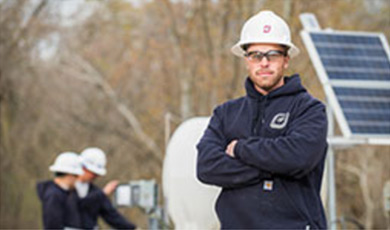
Composite materials are becoming increasingly popular in roller coaster design, thanks to their lightweight and customizable properties. They allow for creative freedom in designing coaster cars and components that require specific shapes and weights. Fiberglass, a common composite used in the coaster industry, is particularly valued for crafting intricate, aerodynamic car designs. Its resistance to moisture and temperature extremes ensures that car exteriors maintain integrity and performance across varying climates.
roller coaster project materials
Beyond the primary materials, the finer details of coaster construction cannot be overlooked. Fasteners, bearings, and wheels play pivotal roles in ensuring the smooth operation of the ride. High-performance polymer-based materials are often employed in the fabrication of wheels and bearings, chosen for their ability to reduce friction and wear. These components must withstand continual stress and, therefore, are rigorously tested to meet industry standards. Bolts and fasteners made of alloys such as stainless steel are preferred for their resilience against rust and their crucial contribution to structural stability.
The expertise required to select and implement these materials is backed by rigorous industry standards and ongoing research. Engineering bodies and safety organizations, such as ASTM International, provide guidelines that inform the materials used throughout the roller coaster construction process. Certification from these authoritative entities not only guarantees compliance but also enhances the trustworthiness of the ride, reassuring both operators and passengers of its safety and reliability.
In summary,
the materials selected for a roller coaster project are instrumental in defining the ride's quality, safety, and appeal. The balance between innovation and reliability must be meticulously maintained, leveraging both advanced and time-tested materials. As technology and materials science evolve, the expertise and insight that guide these selections remain pivotal, promising ever more thrilling and secure experiences for coaster enthusiasts around the world.